SAFETY
SAFETY COMES EASY WHEN YOUR EMPLOYEES ARE LIKE FAMILY.
WE HAVE THE INDUSTRY’S LEADING SAFETY RATINGS. PERIOD.
We take pride in our EMR and our 60-year history of awards and recognition for jobsite safety. And while the awards are nice, that’s not what motivates us. As a family-owned company we’re driven to look after our employees and our partners as though they’re part of our family. Because they are.
For more than six decades, we’ve made, and continue to make, jobsite safety our first priority—every day on every project. Our commitment to jobsite safety is supported by an integrated team of RSA health and safety professionals dedicated to meeting any workplace challenge or site condition by providing programs, policies and training specific to project needs.
OUR SAFETY NUMBERS TELL A STORY
Everyone in this industry talks about their impressive safety record. We’ve got the numbers to back ours up! 0.69 Experience Modifier Rate (EMR). Over 1,800 Safety Training Sessions Per Year. 0.66 Total Recordable Incident Rate (TRIR).
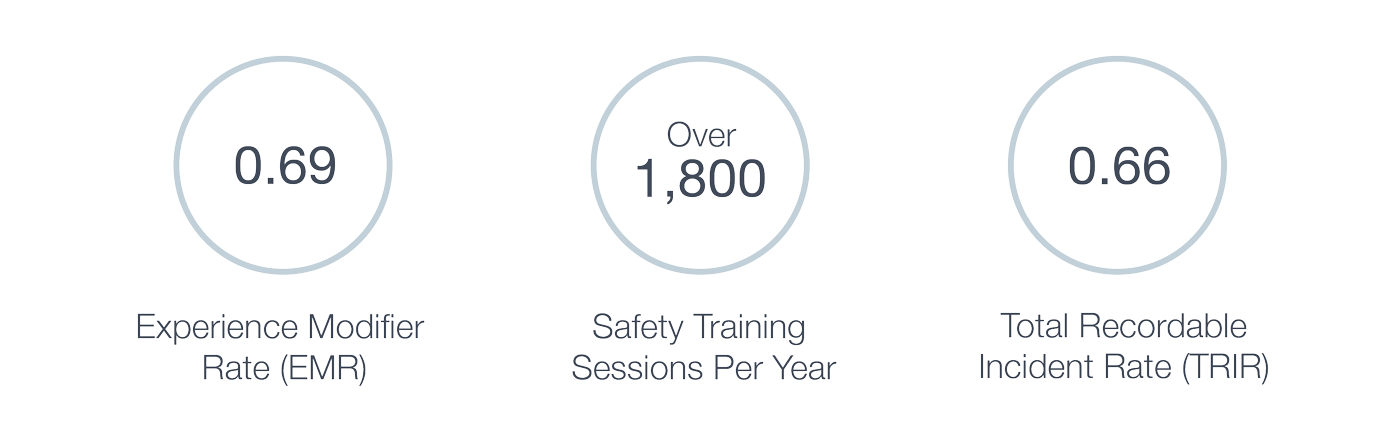
Commitment
We implement our comprehensive corporate safety program on all RSA Construction Group project sites. Based on a philosophy of training and accountability, our commitment begins with top management, extends through all levels of supervision and is regularly communicated to all craft personnel. Our supervisors also receive ongoing training to improve skills and maintain safety excellence. Our professional staff develops policies and implements programs to ensure safety remains our top priority—every day on every project.
Assurance
Workplace safety on project sites and in our offices is ingrained in the RSA corporate culture. More than 50 RSA Construction Group experienced safety and health professionals work with each production team to evaluate safety measures for each potential project. During construction, safety and supervisory staff continually monitor the work environment to identify and eliminate potential hazards and assure full regulatory compliance. RSA is highly experienced working in a variety of industries regulated by OSHA, MSHA, Bureau of Reclamation, DOT, Corps of Engineers and others.
Proactive
We take a proactive approach to loss control, identifying safety issues before they occur using a customized safety audit system. Workforce candidates must pass a pre-employment substance abuse screening, and our Substance Abuse Policy includes post-accident and random screenings. New employees participate in an introductory jobsite safety orientation and all craft employees participate in weekly toolbox safety meetings, with task-specific safety briefings given at the beginning of each work day. Combined with our comprehensive corporate safety program, this training supports our top-down commitment to safety as our first priority.